Can a Robotics Engineering Company in Alabama Make Your Steel Company More Sustainable?
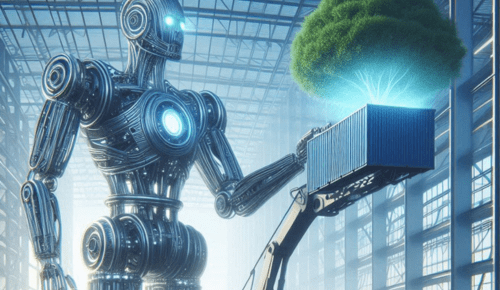
Sustainability in steel manufacturing is more than just a trend—it’s a necessity. Companies are under pressure to reduce waste, lower emissions, and optimize energy use while maintaining high production levels. A robotics engineering company in Alabama can help steel manufacturers meet these goals by integrating advanced automation into their operations.
Precision Robotics Reduce Scrap Waste in Steel Production
Every piece of wasted steel represents lost resources and increased costs. Robotic systems can dramatically reduce scrap by performing precise cutting, welding, and material handling tasks with minimal error. Unlike manual processes that rely on human precision, robotics ensure consistent execution, reducing the likelihood of mistakes that lead to excess material waste.
An Alabama robotics engineering company can design and implement automated solutions that improve efficiency in steel fabrication. These robots can calculate exact material requirements, cut with incredible accuracy, and sort scrap efficiently for recycling. As a result, manufacturers see a noticeable drop in waste, translating into both financial savings and a reduced environmental footprint. With smarter material usage, steel plants move closer to sustainability without compromising productivity.
Robotic Systems Optimize Energy Usage in Steel Mills
Energy consumption in steel production is massive, but robotic automation can introduce efficiency that significantly lowers power usage. Robotics enhance the timing and coordination of industrial machinery, ensuring that equipment runs only when necessary. Intelligent automation also identifies energy-draining inefficiencies and corrects them in real time.
A robotics engineering company in Alabama can develop custom systems that adjust operations based on real-time data. These robotic solutions can optimize furnace heating cycles, improve conveyor efficiency, and even monitor auxiliary equipment to prevent unnecessary energy draw. With automation handling energy-intensive tasks more effectively, steel manufacturers can reduce consumption, cut costs, and lower their environmental impact.
Automated Processes Lower Emissions from Steel Manufacturing
Steel production is one of the leading contributors to industrial emissions, but robotics can help curb the environmental impact. Automated systems refine combustion processes, monitor gas emissions, and ensure furnaces operate within the most efficient parameters. Reducing unnecessary fuel burn lowers carbon output without affecting production speed.
An Alabama robotics engineering company can integrate robotic arms and AI-driven monitoring systems to optimize material handling and heat application, preventing excessive emissions. Additionally, automated air filtration systems can capture and neutralize pollutants more effectively than traditional methods. With robotics in place, steel plants can operate at full capacity while producing fewer harmful emissions.
Intelligent Robotics Minimize Resource Overconsumption in Alloy Processing
Alloy processing requires a careful balance of raw materials, and small miscalculations can lead to wasted resources. Robotics introduce intelligent precision, ensuring that only the necessary amount of each component is used. By eliminating guesswork, manufacturers can maximize material efficiency and reduce excess consumption.
A robotics engineering company in Alabama can implement automation that adjusts alloy composition in real-time based on quality control feedback. These systems analyze metal properties during processing and make instant modifications, preventing the need for rework or excessive material use. With robotic precision managing alloy production, steel companies can achieve sustainability goals while maintaining product consistency.
Consistent Robotic Performance Enhances Steel Quality and Sustainability
Fluctuations in product quality often lead to wasted batches and costly reprocessing. Robotics eliminate inconsistencies by maintaining precise control over every stage of steel production. Automated welding, cutting, and molding ensure each piece meets exact specifications, reducing the risk of defects.
By integrating robotic solutions from an Alabama robotics engineering company, steel manufacturers can minimize quality deviations that lead to rejected products. Consistent performance means fewer resources are spent on rework, and energy isn’t wasted on unnecessary corrections. Higher-quality steel produced with less waste enhances sustainability while meeting customer demands for durability and precision.
Robotics Extend Machinery Lifespan Promoting Sustainable Operations
Manufacturing equipment endures heavy wear and tear, leading to frequent maintenance and early replacement. Robotics can help extend the lifespan of industrial machinery by optimizing operational efficiency and reducing unnecessary strain on mechanical components. With automated systems monitoring equipment performance, manufacturers can proactively address minor issues before they escalate into costly breakdowns.
A robotics engineering company in Alabama can develop predictive maintenance solutions that use sensors and AI-driven analytics to detect potential failures. By preventing excessive wear and optimizing machine usage, these robotic systems reduce downtime, minimize repair costs, and decrease the need for new equipment. Sustainable manufacturing isn’t just about reducing waste—it’s also about making the most of existing resources.
Custom Automation Cuts Down Water Usage in Steel Fabrication
Water plays a critical role in cooling and processing steel, but excessive usage leads to waste and environmental strain. Robotics introduce smarter water management solutions by controlling flow rates, monitoring consumption, and recycling used water more efficiently. Automated cooling systems adjust water application in real-time, ensuring only the necessary amount is used.
An Alabama robotics engineering company can implement robotics-driven filtration and recycling systems that significantly reduce water waste in steel fabrication. These systems recover and treat water for reuse, minimizing the demand for fresh resources. By reducing overall consumption, steel manufacturers can lower costs while meeting sustainability standards without sacrificing production efficiency.