Erik Hosler on How Chiplet Ecosystems Are Enabling Supply Chain Resilience in Packaging
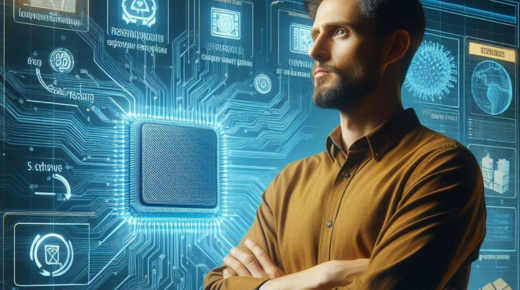
The semiconductor industry has faced growing pressure to improve supply chain agility as global disruptions, geopolitical tensions and material shortages continue to challenge traditional models. In this environment, chiplet-based design has emerged not only as a performance enabler but also as a strategic solution for enhancing supply chain resilience. Erik Hosler, a champion of modular semiconductor architectures, recognizes how chiplet ecosystems allow manufacturers to decouple sourcing and accelerate integration across vendors, substrates and manufacturing partners.
This shift toward modularity is reshaping supply chain design. Instead of relying on single monolithic builds, manufacturers are embracing decentralized sourcing, more flexible packaging flows and scalable design reusability to withstand volatility and maintain competitiveness.
The Problem with Traditional Monolithic Models
Historically, semiconductor design has been centered around large, monolithic System-On-Chip (SoC) designs that integrate all functions into a single die. While this approach has advantages in power and latency optimization, it also creates major bottlenecks in the supply chain. A delay in one functional block, such as memory or Input/Output, can stall the entire product. Yields at advanced process nodes can also drive up costs, and any defect means scrapping the full device.
Recent global supply chain disruptions have magnified these risks. Fab capacity shortages, shipping delays and export restrictions have made it clear that monolithic models are ill-suited to handle supply volatility. A more modular approach is needed, one that separates functional domains and allows sourcing flexibility, risk segmentation and faster design cycles.
Chiplet Ecosystems as a Modular Supply Solution
Chiplets provide a powerful alternative to monolithic SoCs by disaggregating components into smaller dies that can be independently designed, manufactured and tested. These dies are then integrated into a single package using 2.5D or 3D interposers and advanced packaging techniques.
From a supply chain perspective, this model introduces several strategic advantages. It allows companies to work with multiple foundries and vendors across process nodes. A logic chipset might be built on a cutting-edge node, while an analog or memory chipset comes from a mature node. This diversification reduces dependence on any single supplier and improves access to constrained capacity.
Chiplets can be reused across product lines, reducing the need to requalify new Intellectual Property (IP) or fabricate full systems. This shortens development time and lowers the risk of design delays. By creating a library of validated chiplets, companies can respond faster to changing market needs and roll out variants with minimal redesign.
Flexible Packaging with Standardized Interfaces
Standardization is essential for chipset ecosystems to support supply chain resilience. Interconnect protocols such as UCIe, AXI and proprietary die-to-die links provide the foundation for interoperability across dies from different vendors.
With standardized interfaces, companies can source chiplets from third parties and confidently integrate them into known packaging configurations. Packaging houses can stock common interposer designs and substrates, enabling faster assembly and reducing time to volume.
Standardized interposers also simplify supply planning. Rather than custom-routing each package, designers can rely on known templates and validated flows that scale across product families. This lowers engineering overhead and improves alignment between design teams and contract manufacturers.
The result is a more adaptable, reusable packaging flow that decouples sourcing decisions from system-level design timelines.
Enabling Regional Sourcing Strategies
Chiplet-based systems also support regionalized sourcing strategies that improve resilience in the face of geopolitical and logistical disruptions. By segmenting dies by function and foundry, companies can shift sourcing for specific chiplets without overhauling entire product architectures.
For instance, a supply-constrained chipset from one geography can be replaced with a functionally equivalent die from another region, assuming interface standards are met. This capability supports multi-sourcing strategies and gives procurement teams more leverage when negotiating with suppliers.
Packaging flexibility also allows the final assembly to be conducted closer to end markets, reducing freight time and exposure to cross-border regulatory issues. Regional packaging centers can stock standard interposers and integrate chiplets as they arrive, shortening lead times and enabling localized product customization.
Erik Hosler explains, “Working with new materials like GaN, SiC, graphene and other two-dimensional materials is unlocking new potential in semiconductor fabrication, and with it, new semiconductor equipment platforms will likely be required, like accelerator-based light sources.” This kind of material and platform flexibility mirrors the agility that chiplet ecosystems bring to supply chains. By modularizing both function and source, companies can adapt their operations without compromising performance or design integrity.
Risk Mitigation Through Supply Decoupling
Another benefit of chiplet ecosystems is the ability to isolate and mitigate risks within the supply chain. If a defect or delay arises in one chiplet, it does not affect the rest of the system. Known good die testing ensures that only validated components are integrated, improving overall yield and reducing waste.
This decoupling of functional domains also improves production scalability. High-yield chiplets can be stockpiled and combined with just-in-time deliveries of complementary dies. Manufacturers can maintain flexibility in production volumes, scaling specific product variants depending on market demand.
In critical sectors like defense or automotive, where traceability and qualification are paramount, modular packaging supports better documentation and lifecycle management. Each chiplet can be tracked individually, tested to specific standards and replaced without recertifying the entire device.
Ecosystem Collaboration and Foundry Enablement
The strength of a chiplet-based supply chain depends on collaboration across the ecosystem. Foundries must provide known goods that meet interoperability standards. OSATs must offer flexible packaging flows that support chiplet mixing. EDA vendors must deliver simulation tools that model system behavior across dies and interposers.
As these capabilities mature, industry groups and open standards bodies are accelerating progress. UCIe has emerged as a widely supported standard for die-to-die communication. Multi-vendor demonstration platforms are proving the feasibility of interoperable chiplets in real-world systems.
By aligning around common platforms and protocols, the industry is creating a shared infrastructure that supports not just performance scaling but operational resilience. This collective effort is laying the groundwork for a new generation of supply chain-ready packaging flows.
Building Smarter Resilience Through Modularity
The shift toward chiplet ecosystems is not just a technical trend; it is a strategic response to an increasingly unpredictable supply environment. Modular design, standard interfaces and packaging flexibility allow companies to isolate risk, source strategically, and respond quickly to market or geopolitical disruptions.
The broader industry consensus around scalable architectures and cross-domain innovation reflects a growing understanding that resilience must be designed into systems from the start. Chiplet ecosystems, with their ability to mix, match and modularize, are offering a blueprint for how packaging can evolve to meet both performance and supply chain demands.
As the global semiconductor market continues to face uncertainty, companies that embrace chiplet modularity will be better positioned to thrive. They will deliver faster, recover quicker and scale smarter, driven by a packaging strategy that turns complexity into control.